In the processing of Suzhou CNC machining center, it is very important that it is sure to prevent the CNC machining center from colliding when programming and manipulating the machining. Because the value of CNC machining centers is quite high, ranging from a few hundred thousand yuan to more than one million yuan, it is difficult to repair and costly. However, the occurrence of collisions is affirmative and can be prevented. It may be summarized as the following points.
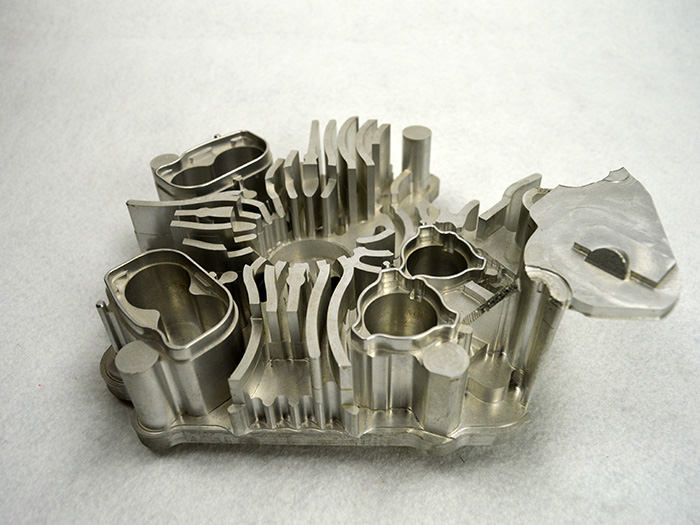
1. Using computer simulation simulation system
With the development of computer skills, CNC machining education is not parked, CNC simulation simulation systems are more and more, and its performance is improving. Therefore, it can be used to start the inspection process and watch the activity of the tool to determine if it is possible to collide.
2, using the simulation of the CNC machining center to show performance
Usually more advanced CNC machining centers have graphical display performance. After entering the program, you can call the graphics to simulate the performance, and view the tool's active trajectory in detail to check if the tool and the workpiece or fixture are likely to collide.
3. Using the dry running performance of the CNC machining center
The accuracy of the trajectory of the tool can be verified by utilizing the dry running performance of the CNC machining center. After the program is input into the CNC machining center, it is possible to install the tool or workpiece, and then press the dry run button. At this time, the spindle does not rotate, and the workbench automatically runs according to the program path. At this time, it is possible to find out whether the tool is likely to be in contact with the workpiece or the fixture. bump. However, in this case, it must be ensured that the tool cannot be loaded when the workpiece is mounted; when the tool is installed, the workpiece cannot be loaded, or a collision will occur.
4, the use of CNC machining center locking performance
Typical CNC machining centers have locking performance (full lock or single axis lock). When the program is input, the Z axis is locked, and the coordinate value of the Z axis can be used to infer whether a collision will occur. The use of this performance should avoid the operation of tool change, or the program can not pass.
5, the coordinate system, the tool compensation configuration must be accurate
When starting a CNC machining center, you must configure the CNC machining center reference point. The working coordinate system of the CNC machining center should be maintained with the programming time, and the Z-axis target is more and more. If the mistake is made, the possibility that the milling cutter will collide with the workpiece is quite large. The rest, the configuration of the tool length compensation must be accurate, otherwise it is either empty machining or collision.
6, increase programming skills
Programming is a crucial part of CNC machining. Increasing programming skills may help prevent unwanted collisions at a large level.
For example, when milling the workpiece cavity, when the milling is completed, the required milling cutter is quickly retracted to 100mm above the workpiece. If programmed with N50 G00 X0 Y0 Z100, the CNC machining center will link the three axes, and the milling cutter may be related to the workpiece. Collision occurs, the tool and the workpiece are damaged, and the accuracy of the CNC machining center must be affected. At this time, the following program N40 G00 Z100; N50 X0 Y0 can be selected; that is, the tool first retreats to 100mm above the workpiece, and then returns to the programmed zero point, so that it will not collision.
In short, in charge of the programming skills of the cnc machining center, it can better improve the processing efficiency, processing quality, and prevent unnecessary errors in the processing. This demand continues to sum up experience in the practice, and keeps rising, thus further strengthening the programming and processing strength.