Need to pay attention to the process of CNC lathe processing. The machining process of CNC lathe is similar to the machining process of ordinary lathe, but since CNC is a single clamping and continuous automatic machining completes all turning operations, we should pay attention to the following aspects.
1. Correct selection of cutting amount
Regarding high-efficiency metal cutting, the raw materials to be processed, cutting equipment, and cutting conditions are three factors. These decisions are time, tool life and processing quality. Economically useful processing methods must be the correct choice of cutting conditions.
Three factors of cutting conditions: cutting speed, feed rate and depth of cut directly cause damage to the tool. Along with the increase in cutting speed, the tip temperature will rise and mechanical, chemical, and thermal wear will occur. Increased cutting speed reduces tool life by 1/2.
The feed condition and the wear behind the tool occur within a very small boundary. However, the feed rate is large, the cutting temperature rises, and the wear at the back is large. It has less effect on the tool than the cutting speed. Effect of cutting depth on the tool Although there is no cutting speed and large feed rate, in the case of small depth cutting, the hardened layer of the material to be cut will also affect the life of the tool.
The user should select the cutting speed to be used according to the raw material to be processed, the hardness, the cutting form, the type of raw material, the feed amount, and the depth of cut. The following table:
The selection of suitable processing conditions is essentially selected for these factors. It is the condition of dreams to have a lawful, stable wear and tear to reach life.
However, in the essential homework, the choice of tool life is related to tool wear, machine size change, surface quality, cutting noise, heat processing, and so on. When affirming the processing conditions, the demand is discussed according to the essential conditions. For difficult-to-machine materials such as stainless steel and heat-resistant alloys, it is advisable to use a coolant or a rigid blade.
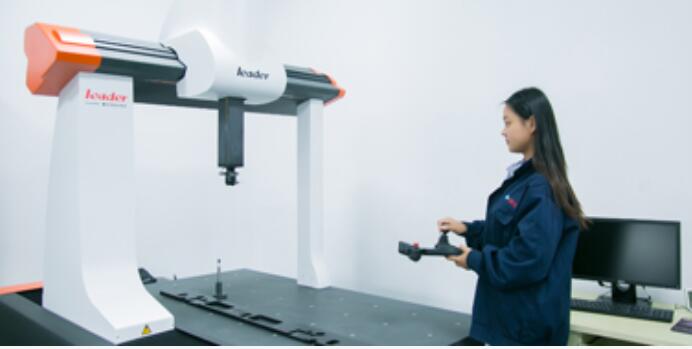
2. Choose the right tool
1) When roughing the car, it is necessary to select a tool with high strength and durability to meet the requirements of large back feed and large feed amount during roughing.
2) When finishing the car, it is necessary to select the tool with high precision and durability to ensure the processing precision.
3) In order to reduce the time of tool change and simple tool setting, the machine clamp and machine clamp blade should be used.
3. Correct selection of fixtures
1) Although the general fixture is used to clamp the workpiece, the special fixture is prevented from being selected;
2) The part positioning reference coincides to reduce the positioning deviation.
4. Affirmation of processing routes
The machining route is the active trajectory and target of the tool relative to the part during the index control machine tool processing.
1) should ensure the processing accuracy and surface roughness requirements;
2) Despite the reduction of the machining route, reduce the tool idle travel time.
5. Processing route is related to machining allowance
At present, under the condition that the numerical control lathe has not yet reached the universal application, it is usually necessary to place too much margin on the blank, and the unique amount of the forged and cast hard skin layer is placed on the ordinary lathe for processing. If you must use CNC lathe processing, you need to pay attention to the sensitive placement of the program.
6. Fixture installation points
The connection between the hydraulic chuck and the hydraulic clamping cylinder is currently done by means of a tie rod. The hydraulic chuck clamping points are as follows: First, remove the nut on the hydraulic cylinder by moving the handle, remove the pull tube, and pull it out from the rear end of the spindle, and then remove the chuck by using the hand to remove the chuck.
The wiper on the tool refers to a small section of the tool that is parallel to the tool tip at the back of the tool blade. The blade is used for the secondary cutting after the cutting of the blade. It is equivalent to the finishing process. Increasing the surface roughness of the workpiece is often used on the tool for finishing.