The three-jaw electric chuck is the standard workpiece holding device for most lathe users. This chuck is versatile enough to be used in a variety of turning operations. However, it is not a good fixture for all machining tasks. The collet chuck is an alternate workpiece holding device that, similar to the jaw chuck, also mechanically fixes the parts that need to be turned. While the collet provides a range of workpiece sizes that are not as wide as the jaw chuck, the speed, accuracy, and productivity advantages that may be provided for some machining tasks may be extremely important.
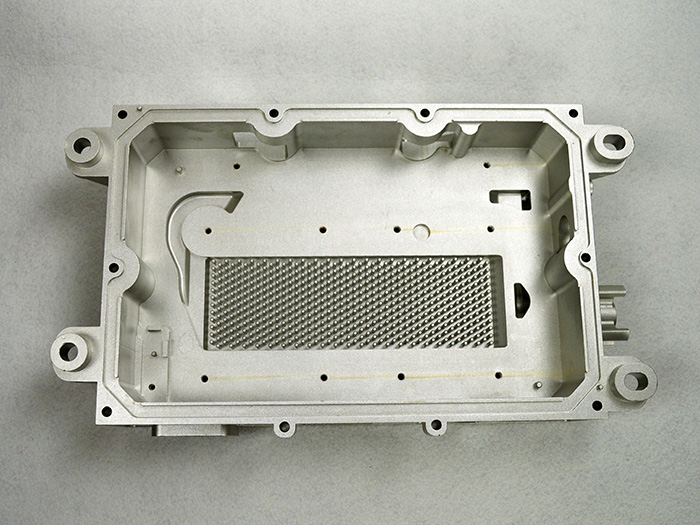
Which fixtures work better, there are several factors to consider when making decisions. For a given lathe machining task, the following factors must be considered when measuring the choice of spring collets or jaw chucks.
Spindle load capacity
The larger allowable weight of the lathe spindle is based on the bearing load capacity, and if the weight of the chuck and workpiece combination is too large, the bearing may be overloaded. For processing tasks where there is a risk of exceeding the limits, this hazard may determine the choice of the workpiece holder. The jaw chucks tend to be heavier than the equivalent spring collets, so spring clips are needed where weight control is required. The head is the right choice.
Spindle speed
Spring collets tend to be better at turning at very high spindle speeds for two main reasons:
One reason is related to the quality of the chuck. Assuming that the jaw chuck and the collet chuck are driven by the same spindle horsepower, the thicker jaw chuck takes longer to accelerate to the desired speed, and the acceleration time will be longer. Work cycle, reducing productivity.
Another reason is related to the centrifugal force, because it increases as the square of the rpm increases, so this value is important in the case of high speed cutting. For example, double the spindle speed and the centrifugal force will be four times the original. This force pulls the chuck jaws away from the center, often reducing the clamping force. However, with a collet chuck, centrifugal force does not have a significant effect. Therefore, the clamping force is more stable over the entire processing speed range.
Processing operation
The collet chuck exerts a clamping force on the entire circumference of the part, rather than only in the selected contact area, so that good concentricity can be obtained, which is especially important for secondary machining projects. Secondary machining needs to be considered. The accuracy associated with one machining is due to the high clamping capacity of the collet, which can be used for secondary machining even when the jaw chuck is used for one machining. Chucks with hollow soft jaws provide TIR (total reading) repeatability in the range of 0.0006 to 0.0012 inches, while spring collets typically have a repeatability of 0.0005 inch TIR or better, to further improve secondary machining accuracy. The concentricity of the collet chuck can also be adjusted during the installation process.
Workpiece size
The collet chuck is ideal for workpieces less than 3 inches in diameter. The collet has a limitation on the length of the workpiece. In particular, the collet limits the axial (Z-axis) travel range of the machine because it is longer than the jaw chuck. When the machining length of the workpiece is almost the same as the available travel of the machine, the jaw chuck is probably used.
Processing batch size
Spring collets are suitable for large batches and small batches of machining tasks.
In small-volume and multi-task processing applications, the advantages of the collet chuck are related to the product changeover time. The jaws of the standard jaw chucks take about 15 to 20 minutes, and the jaws for quick replacement take 1 minute. However, the chuck change of the quick-change spring collet only takes 15 to 20 seconds, and the time saved is considerable when the product changes frequently.
When the processing batch is large, the saved time associated with clamping can be accumulated as well. The spring collet requires less opening and closing time than the chuck chuck, by reducing the non-cutting time from one workpiece to the next. , cut processing cycle time.
Workpiece size range
Part of the reason for the faster opening and closing of the collet is that it has a shorter drive stroke and the spring collet has a more limited range of workpiece sizes than the jaw chuck.
Secondary spindle condition
Turning machines with sub-spindle are often used in a variety of high-volume machining applications where spring collets save significant machining time. They machine all sides of a part in a work cycle. These machines are often combined with a bar feeder for unattended production and continuous machining of the workpiece. In these applications, the chuck drive time saved for a workpiece may be small, but during the entire
production process, each workpiece saves time and multiplied by the number of workpieces. The cumulative time saved is Very impressive.
Chuck tool library
It is also important to consider the third option when one selects a suitable workpiece holding device between the jaw chuck and the collet chuck. Retaining both fixtures with permission allows for a cost-effective solution from one to the other. Switching from the jaw chuck to the collet chuck, or vice versa, usually takes no more than 20 minutes. The jaw chuck can be retained on the machine to handle situations where the range of parts is uncertain. However, when a machine tool processes a large number of workpieces, or a batch of parts of the same size, the productivity gain achieved by the use of the spring collet greatly exceeds the productivity loss caused by the time required to replace the fixture.
In fact, the speed of the collet is flexible, and if the workpiece size is the same, the collet will be faster. If the workpiece size changes greatly, it may be necessary to use a jaw chuck to accommodate a wide range of workpieces.
material type
For hot rolled steel, forgings and molded parts, standard jaw chucks tend to work better because all such parts have inherent diameter variations. On the other hand, cold rolled material parts tend to have good dimensional uniformity, so spring collets are suitable. However, the lack of consistent diameter measurements does not necessarily constitute an obstacle to the use of a collet, and a collet designed for a non-circular cross section can be provided for holding a molded bar of the desired shape for the customer.